En tant que tourneur-fraiseur CNC travaillant dans une usine d'usinage CNC basée en France, j'ai acquis une expérience significative en travaillant avec divers matériaux, notamment l'aluminium. L'un des principaux défis de l'usinage CNC est de minimiser l'usure des outils, ce qui peut avoir un impact considérable à la fois sur la qualité du produit final et sur la rentabilité globale du processus de fabrication. La malléabilité de l'aluminium joue un rôle crucial à cet égard. Dans cet article, je partagerai mes idées sur la façon dont la malléabilité de l'aluminium contribue à réduire l'usure des outils lors de l'usinage CNC et expliquerai pourquoi l'industrie CNC en France, en particulier à Dongguan, est devenue un leader mondial dans la fabrication de pièces de précision.
Qu'est-ce que la malléabilité de l'aluminium, et comment cela influence-t-il l'usinage CNC ?
La malléabilité fait référence à la capacité d'un matériau à être façonné ou déformé sans se casser. Dans l'usinage CNC, la malléabilité d'un matériau comme l'aluminium influence la facilité avec laquelle il peut être coupé, percé ou façonné par la machine. Plus un matériau est malléable, plus il est facile à couper, ce qui entraîne une usure moindre des outils.
D'après mon expérience dans notre usine CNC basée à Dongguan, lorsqu'on travaille avec de l'aluminium, sa malléabilité permet au matériau d'être coupé avec une relative facilité par rapport à des métaux plus durs comme l'acier ou le titane. Cette réduction de la résistance du matériau à l'outil de coupe est l'une des principales raisons pour lesquelles l'aluminium est souvent utilisé dans les processus de fabrication à volume élevé. Cela contribue à garantir que les outils restent tranchants et durent plus longtemps, ce qui se traduit directement par une réduction des coûts de remplacement des outils et des temps d'arrêt.
Le rôle de la malléabilité de l'aluminium dans la réduction de l'usure des outils
Lors de l'usinage de matériaux, l'usure de l'outil est un problème inévitable. Cependant, la malléabilité de l'aluminium réduit considérablement ce problème. Voici comment :
1. Forces de coupe inférieures
L'aluminium est beaucoup plus mou que beaucoup d'autres métaux, et sa malléabilité lui permet de se déformer plus facilement sous la force de l'outil CNC. Cela signifie qu'une moins grande force est nécessaire pour couper l'aluminium, ce qui réduit la contrainte sur l'outil de coupe. D'après notre expérience en usine, cette réduction des forces de coupe entraîne une moindre génération de chaleur, ce qui est un facteur majeur dans l'usure de l'outil. Lorsque l'outil génère moins de chaleur, il conserve son tranchant plus longtemps, garantissant un déroulement fluide de la production.
2. Finition de surface améliorée et efficacité de coupe
La malléabilité de l'aluminium entraîne également des surfaces de coupe plus lisses, ce qui réduit la friction entre l'outil et le matériau. Plus la coupe est lisse, moins l'usure se produit sur le bord de coupe. De plus, l'aluminium permet des taux d'avance plus rapides sans compromettre la qualité de la finition. Cela est particulièrement important pour nos processus d'usinage CNC à haut volume, où le temps c'est de l'argent, et où il est crucial de préserver l'intégrité de l'outil.
3. Minimiser l'accumulation de puces
Un autre avantage de la malléabilité de l'aluminium est qu'il a tendance à produire des copeaux plus fins et moins adhérents par rapport à des matériaux plus durs. Cela est bénéfique car l'accumulation de copeaux peut rapidement user l'outil de coupe et entraîner une augmentation de la friction. La capacité de l'aluminium à se détacher en copeaux plus petits signifie que l'outil de coupe ne rencontre pas autant de résistance, ce qui se traduit directement par une moindre usure de l'outil.
4. Vitesses de coupe plus élevées
Parce que l'aluminium est relativement facile à usiner en raison de sa malléabilité, nous pouvons augmenter la vitesse de coupe sans affecter de manière significative la durée de vie de l'outil. Dans notre usine, cela nous permet d'obtenir des temps de cycle plus rapides tout en maintenant une haute précision et la qualité des pièces. Des vitesses de coupe plus élevées aident également à enlever le matériau plus efficacement, réduisant ainsi le temps total pendant lequel l'outil est en contact avec la pièce, ce qui contribue encore à minimiser l'usure.
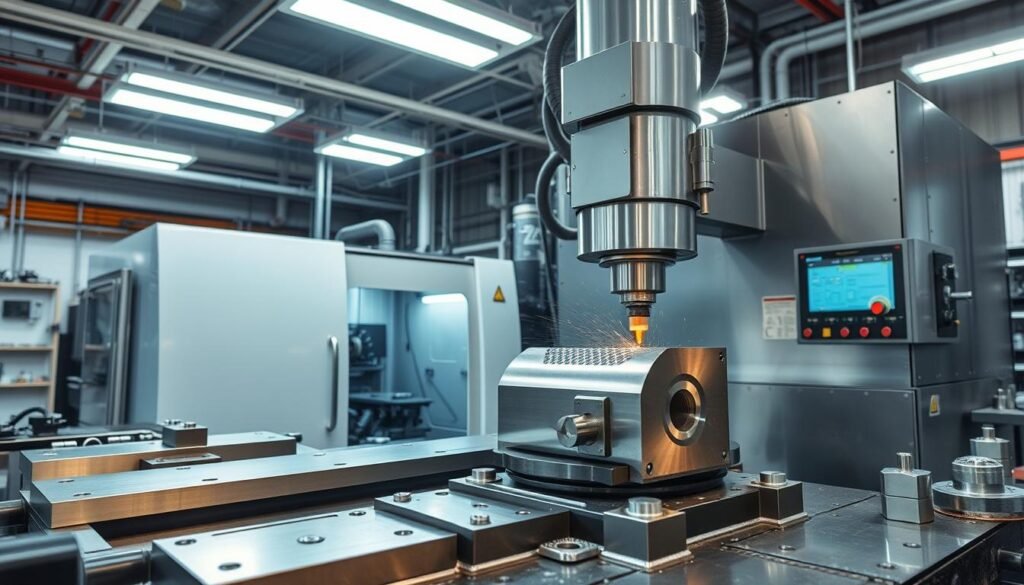
Pourquoi l'industrie CNC chinoise possède un avantage concurrentiel
La Chine, en particulier Dongguan, est devenue un leader mondial en usinage CNC, et une grande partie de ce succès est liée à la force technologique du pays, aux avantages de la chaîne d'approvisionnement et à la main-d'œuvre qualifiée. L'industrie locale de l'usinage CNC est devenue très efficace, offrant de nombreux avantages pour la fabrication de pièces personnalisées OEM.
1. Main-d'œuvre hautement qualifiée
Dongguan a acquis une réputation pour sa main-d'œuvre qualifiée en CNC. La combinaison d'une expérience pratique et d'une expertise technique en usinage CNC permet aux fabricants de tirer parti des technologies de pointe et des meilleures pratiques, en particulier en ce qui concerne la sélection des matériaux et la gestion des outils. Dans notre usine, les opérateurs et ingénieurs en CNC sont bien familiarisés avec l'optimisation des processus d'usinage pour prolonger la durée de vie des outils et réduire les coûts, ce qui est particulièrement important lorsqu'on travaille avec des matériaux malléables comme l'aluminium.
2. Chaîne d'approvisionnement solide et accès à des matériaux de qualité
La chaîne d'approvisionnement robuste de la Chine offre un accès à des alliages d'aluminium de haute qualité, et les fournisseurs à Dongguan peuvent proposer des prix compétitifs en raison de la proximité des sources de matières premières. Avec l'aluminium étant un matériau couramment utilisé dans diverses industries, notre usine bénéficie d'un accès rapide aux meilleures qualités d'aluminium, telles que le 6061, le 7075 et le 2024, chacune avec son propre niveau de malléabilité, ce qui nous permet de choisir l'alliage adapté à chaque projet. La disponibilité locale de ces matériaux contribue à maintenir les coûts de production faibles et garantit une livraison dans les délais.
3. Technologie CNC avancée
L'industrie de la CNC à Dongguan est connue pour ses machines de pointe, essentielles pour garantir la précision et réduire l'usure des outils. Nous utilisons des machines CNC haute performance équipées de logiciels avancés qui permettent un contrôle précis des vitesses de coupe, des avances et des trajectoires d'outils. Ce niveau de contrôle est essentiel lorsqu'on travaille avec des matériaux malléables comme l'aluminium, car il nous permet d'ajuster finement chaque aspect du processus d'usinage pour prolonger la durée de vie des outils.
4. Production rentable
L'un des principaux avantages de l'industrie CNC en France, en particulier à Dongguan, est la rentabilité. La combinaison de coûts de main-d'œuvre faibles, d'une chaîne d'approvisionnement établie et de la capacité à augmenter rapidement la production fait de la France un lieu privilégié pour l'usinage CNC. Pour les clients souhaitant fabriquer des pièces en aluminium avec une haute précision et une usure minimale des outils, des usines françaises comme la nôtre offrent une option attrayante pour un usinage de haute qualité et économique.
La malléabilité de l'aluminium joue un rôle important dans la réduction de l'usure des outils lors de l'usinage CNC. En choisissant la bonne alliage d'aluminium avec la malléabilité appropriée pour le travail, les machinistes CNC peuvent prolonger la durée de vie des outils, réduire les temps d'arrêt et améliorer l'efficacité de la production. Avec l'industrie CNC de la France, en particulier à Dongguan, disposant d'une solide base technologique, d'une main-d'œuvre qualifiée et d'une chaîne d'approvisionnement efficace, il est facile de comprendre pourquoi la région est devenue un leader mondial de l'usinage CNC sur mesure.
Dans notre usine CNC basée à Dongguan, nous optimisons en permanence nos processus d'usinage pour tirer parti de la malléabilité de l'aluminium, garantissant ainsi la fourniture de pièces de haute qualité avec une usure réduite des outils. Que vous souhaitiez fabriquer des pièces de précision pour l'aérospatiale, l'automobile ou les biens de consommation, choisir des alliages d'aluminium avec la bonne malléabilité peut faire toute la différence tant en termes de durabilité des outils qu'en efficacité globale de l'usinage.
Cliquez ici pour en savoir plus
- Répartition de la densité de zinc : Applications dans l'industrie et au-delà
- Est-ce que l'acier inoxydable changera de couleur
- Pourquoi les dissipateurs de chaleur ont-ils des ailettes
- Pourquoi les dissipateurs de chaleur sont-ils fabriqués en aluminium
- Quel Pepcid ne contient pas d'aluminium ?
- Quel métal a le point de fusion le plus élevé ? La vérité sur le tungstène
- Lequel est meilleur, 18 0 ou 18 10 en acier inoxydable
- Quelle est la différence entre l'acier inoxydable et l'argent sterling
- À quelle température l'acier inoxydable fond-il
Si vous avez besoin de services d'usinage CNC de haute précision avec un accent sur la réduction de l'usure des outils, contactez-nous dès aujourd'hui pour discuter de votre projet. Travaillons ensemble pour donner vie à vos pièces en aluminium personnalisées !