W dynamicznej dziedzinie frezowania CNC w fabrykach OEM, the selection of the right foam material is a critical determinant of product quality and production efficiency. This article delves deep into the insights gleaned from the CNC –; centric Reddit forum, offering in –; depth knowledge to optimize your manufacturing processes.
Tooling Foam: The Workhorse of CNC Milling
Tooling foam is a staple in CNC milling projects. Many industry experts on the forum suggest capping the density at 20#. Opting for a higher density, jak na przykład 50#, can lead to an undesirable weight increase. Consider a dashboard fabricated from 50# piana; its excessive weight could render it impractical. Conversely, 18# foam has emerged as a popular choice for model –; making. It strikes an excellent balance between density and workability, allowing for intricate designs and smooth finishes.
If your project demands larger foam components, fret not. Bonding foam blocks together is a viable solution. Begin by meticulously blowing off any dust from the joining surfaces. Następnie, apply 3M Super77 adhesive evenly, ensuring complete coverage. Let the adhesive dry to a tacky consistency before firmly pressing the foam pieces together. This simple yet effective method can significantly expand the possibilities of what you can create with tooling foam.
Roofmate (XPS): A Budget –; Friendly Option with Caveats
Roofmate, an extruded polystyrene foam (XPS), has gained traction for its cost –; effectiveness. Widely available at local hardware stores, it offers an attractive machining advantage. The surface finish achieved with Roofmate is often quite impressive, making it suitable for projects where aesthetics matter.
Jednakże, it’;s essential to be aware of its limitations. Roofmate is not as durable as some other foam options. A simple scratch from a fingernail can leave a mark, highlighting its vulnerability to wear and tear. As such, it’;s best suited for short –; term or low –; stress applications where longevity isn’;t a primary concern.
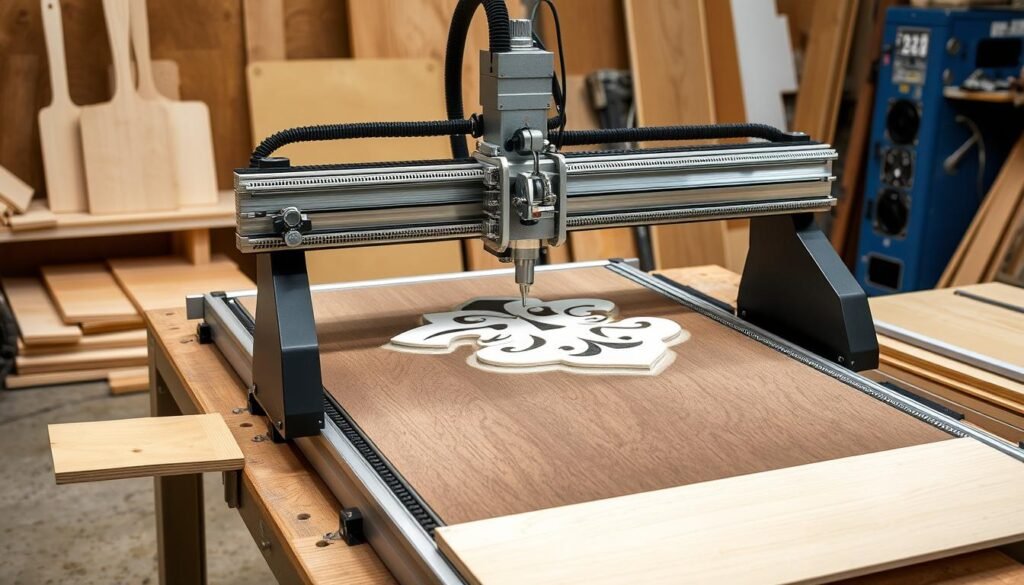
High –; Density Foams for Precision Work
When it comes to crafting highly detailed components like dashboards, high –; density foams are the way to go. Tool board foams with a density of 30Lb+ are specifically designed to meet the demands of intricate designs. These foams can capture the finest details during the CNC milling process, ensuring a precise and professional finish.
But there’;s a catch. High –; density foams typically don’;t come in large blocks. Zamiast, they need to be assembled by bonding smaller pieces together using epoxy glue. This process requires patience and precision but is well worth the effort for the superior results it yields.
High –; Density Polyurethane (HDU): The Premium Choice
High –; density polyurethane (HDU) stands out as a top –; tier option for CNC milling. It boasts excellent machining properties, making it a favorite among manufacturers seeking high –; quality output. One of its notable advantages is the ease of dust management during the milling process. This not only contributes to a cleaner working environment but also reduces the risk of dust –; related issues that could affect the final product.
HDU comes in a range of densities, each offering different benefits. Generally, the higher the density, the better the surface finish of the milled product. Jednakże, this comes at a cost. Higher –; density HDU is more expensive, so it’;s crucial to find the right balance between quality and cost for your specific projects.
To determine the optimal HDU density for your needs, we recommend reaching out to local foam or plastic suppliers. Request sample packs and conduct thorough testing. This hands –; on approach will enable you to evaluate the performance of different densities and make an informed decision based on your project requirements.
Wniosek: Making Informed Choices for Success
As an OEM factory engaged in CNC milling, understanding the nuances of different foam materials is paramount. Whether you’;re working with the versatile 18# tooling foam, the budget –; friendly Roofmate, or the high –; performance HDU, each material has its unique strengths and applications.
By carefully considering the specific requirements of your projects, such as design complexity, durability needs, and budget constraints, you can make informed decisions that will enhance the quality of your products and drive the success of your OEM factory. Stay tuned for more CNC milling insights and tips as we continue to explore the ever –; evolving world of manufacturing materials.