Nhôm là một trong những kim loại được sử dụng phổ biến nhất trong gia công CNC, Được đánh giá cao cho bản chất nhẹ của nó, khả năng chống ăn mòn tuyệt vời, và tính linh hoạt. Tuy nhiên, one of the key properties that set aluminum apart from other metals is its malleability. This characteristic has profound implications for how CNC machining operations are carried out. As an experienced CNC machinist, I’ve encountered firsthand how aluminum’s malleability impacts everything from tool wear to cutting speeds, and even the overall precision of the final product. In this blog, I’ll walk you through the essential details of aluminum’s malleability, and how it affects our daily work in the CNC machining shop.
What is Malleability and Why Does It Matter?
Malleability refers to a material’;s ability to be shaped or deformed without breaking or cracking. Đối với nhôm, this means it can be easily formed into complex shapes under controlled conditions without losing integrity. Malleability is one of the reasons aluminum is so popular in industries ranging from automotive to aerospace, where complex, lightweight parts are in high demand.
From a CNC machining perspective, malleability is both an advantage and a challenge. On the one hand, it means we can machine intricate and detailed parts with relative ease. Mặt khác, it can lead to some specific issues that need to be carefully managed to ensure the parts are made with high precision.
How Malleability Affects CNC Machining Operations
1. Tool Wear and Longevity
Aluminum’s malleability can lead to faster tool wear, especially during high-volume machining. As the material is more likely to flow and deform, the cutting edges of tools can quickly become dull, especially when machining softer grades of aluminum. In my experience, we’ve found that using carbide tools with coatings designed for non-ferrous metals helps improve tool longevity. Ngoài ra, maintaining proper cutting speeds and feeds, based on the specific alloy we’re machining, is crucial to prevent excessive tool wear.
Mẹo: Regularly inspect and replace tools to prevent inconsistent finishes or dimensional inaccuracies.
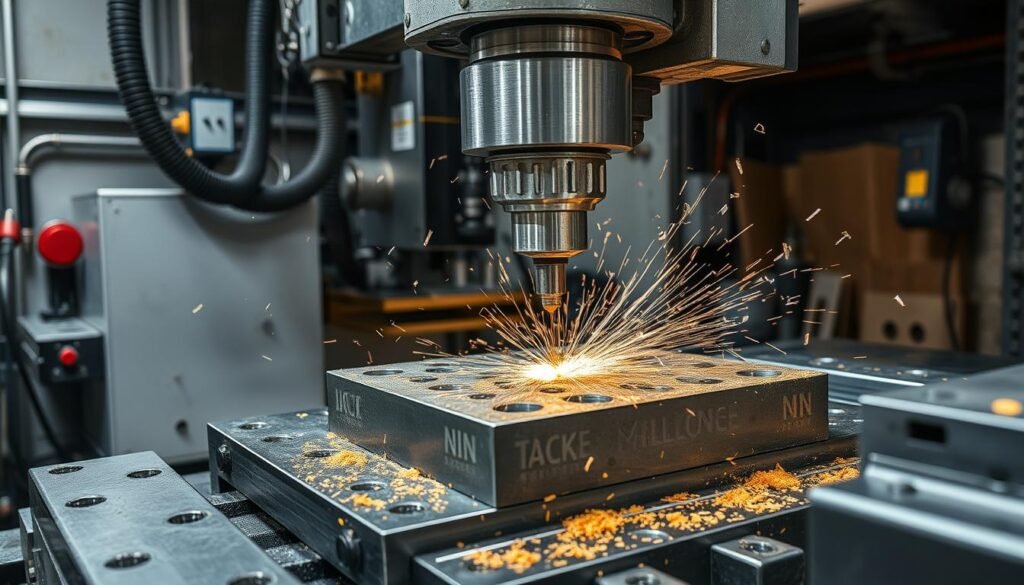
2. Cutting Speeds and Feeds
Malleable aluminum requires careful attention to cutting speeds and feeds. When the material is softer, using too high of a cutting speed can result in material buildup on the cutting edges, leading to poor finishes and tool damage. Conversely, using too low of a cutting speed can increase friction and heat, which can also cause material deformation or stickiness on the tool.
Based on my shop’s experience, we’ve found a balance by using moderate cutting speeds combined with a higher feed rate, which helps prevent aluminum from “;gumming up”; the cutting tool. This balance ensures a cleaner cut and longer tool life, especially when working with alloys like 6061.
Mẹo: Adjust your cutting parameters based on the specific aluminum alloy you’;đang làm việc với. Softer alloys require different settings compared to harder grades.
3. Tolerances and Precision
Achieving tight tolerances when machining aluminum can be challenging due to its malleability. The material can shift or distort under the pressure of cutting forces, which may lead to dimensional inconsistencies. This is especially true with softer aluminum grades, which are more susceptible to deformation during machining.
To combat this, we often use techniques such as precise clamping and using coolant or lubrication to reduce the heat buildup, which can otherwise lead to dimensional shifts. Ngoài ra, ensuring the machine tool is properly calibrated and maintaining stable machining conditions are key to achieving accurate results.
Mẹo: Use rigid clamping systems and ensure the workpiece is properly supported to minimize movement during machining.
4. Hoàn thiện bề mặt
Aluminum’s malleability means it can produce smooth, high-quality surface finishes if the machining conditions are optimized. Tuy nhiên, if the cutting parameters aren’t properly adjusted, the result can be a rough, uneven surface. Overheating and poor tool selection can cause unwanted marks, burrs, or other imperfections.
In our CNC shop, we often use coolant and lubrication systems to maintain a stable temperature and reduce friction. This helps achieve a consistent surface finish, especially when working with intricate designs or high-precision parts like aerospace components.
Mẹo: Always use the right combination of cutting tools, tốc độ, and lubricants for a smooth finish.
Selecting the Right Aluminum Alloy for CNC Machining
Different aluminum alloys exhibit different levels of malleability, and understanding these properties can significantly impact machining outcomes. Ví dụ, 6061 aluminum is widely used in CNC machining due to its balance of strength and malleability. Mặt khác, alloys like 2024, which are stronger but less malleable, may require different handling techniques to avoid cracking or breaking during the machining process.
As a machinist, it’;s crucial to select the right aluminum alloy for the task at hand. While more malleable alloys are easier to machine, they may not always provide the strength or durability required for certain applications. On the flip side, harder alloys might demand slower cutting speeds or more specialized tooling.
Best Practices for CNC Machining Malleable Aluminum
After years of working with aluminum in various CNC projects, I’;ve gathered several best practices that can help improve the efficiency and quality of your machining operations:
- Use the Right Tools: For softer alloys, carbide tools with coatings such as TiAlN (titanium aluminum nitride) are ideal because they resist wear and heat buildup.
- Optimize Cutting Speeds: Test different cutting speeds and feeds for your specific aluminum alloy to find the sweet spot that ensures optimal results without overheating.
- Regularly Check and Replace Tools: Regular tool inspection is critical to maintain consistent quality and to avoid issues such as dimensional inaccuracies due to worn-out tools.
- Use Coolant and Lubrication: Cooling systems and lubrication are essential to dissipate heat and reduce friction, ensuring that both the tool and material are properly managed during the machining process.
- Understand Material Behavior: Different aluminum alloys behave differently during machining. Ví dụ, trong khi 6061 aluminum is relatively easy to machine, alloys like 7075 can be more difficult and may require slower cutting speeds and specific tools.
Aluminum’;s malleability is a double-edged sword in CNC machining. While it allows for intricate designs and quick adaptations, it also demands attention to detail in terms of tool selection, tốc độ cắt, and process management. From my experience, optimizing machining parameters and selecting the right tools can make a significant difference in both efficiency and quality. As CNC machinists, understanding how aluminum behaves under the conditions of the shop floor is key to delivering the best results every time.
By recognizing the implications of aluminum’s malleability and applying the right machining techniques, we can continue to produce high-quality parts that meet the needs of industries ranging from automotive to aerospace.