As CNC machining professionals, we’re constantly faced with a variety of materials, each with its own unique properties. One material that’s particularly common in our work is aluminum. Known for its lightweight yet strong nature, aluminum’s malleability plays a significant role in how we approach CNC machining, especially when it comes to producing precision parts. In this article, I’ll share insights from my experience working in a CNC machining shop, explaining how CNC machines handle aluminum’s malleability to produce high-precision, custom parts for our clients.
What Makes Aluminum Malleable?
Aluminum’s malleability is its ability to be shaped, bent, or deformed without breaking, which is one of the reasons it is widely used in industries ranging from aerospace to automotive. Malleability in aluminum means that it can undergo significant deformation under stress, which makes it ideal for forming complex shapes. However, this property also presents a unique challenge in the CNC machining process, particularly when precision is paramount.
From a machinist’s perspective, aluminum’s malleability allows it to be easily machined into tight tolerances, but it also means that the material can distort or shift during machining if not properly handled.
How CNC Machines Work with Aluminum’s Malleability for Precision
1. Tool Selection and Material Interaction
One of the first things we consider when machining aluminum is the selection of the right tools. Aluminum is soft and malleable, so the choice of cutting tools can greatly affect the quality of the final product. In my experience, carbide tooling with a coating such as TiN (Titanium Nitride) or TiAlN (Titanium Aluminum Nitride) is ideal for aluminum because these coatings increase tool life and reduce heat buildup during machining.
The malleability of aluminum means that cutting tools can wear down faster, especially during prolonged operations. This makes it essential to use tools designed specifically for non-ferrous metals. High-speed steel tools, while common, aren’t as effective for aluminum, as they tend to get dull more quickly when exposed to the softer material. Carbide, on the other hand, can handle aluminum’s deformation better without compromising on precision.
Tip: Make sure your cutting tools are designed specifically for aluminum to extend their lifespan and maintain cutting accuracy.
2. Cutting Speed and Feed Rate Adjustments
Another crucial aspect of CNC machining for aluminum is adjusting cutting speeds and feed rates. Because aluminum is malleable, the material tends to deform as the cutting tool moves through it. If the cutting speed is too high, the tool can overheat, and the aluminum may begin to stick to the tool, causing surface defects and reducing precision. On the other hand, too low of a cutting speed can cause the tool to “pull” the material, leading to uneven cuts and excessive burr formation.
From my experience, finding the right balance between cutting speed and feed rate is essential for achieving precision. For example, when machining soft aluminum alloys like 6061, we tend to use higher feed rates and slightly lower cutting speeds to ensure the material doesn’t deform too much. In contrast, harder alloys like 7075 require a slower feed rate and lower cutting speed to ensure the integrity of the part is maintained.
Tip: Always adjust your CNC machine’s cutting parameters based on the specific aluminum alloy you’re working with to ensure optimal performance.
3. Managing Heat and Friction
Aluminum’s malleability makes it more prone to heat buildup during machining. The softer the material, the more it will deform under heat, which can lead to dimensional inaccuracies. CNC machines equipped with high-quality cooling and lubrication systems are essential for managing this issue. By maintaining a consistent flow of coolant, we can ensure that the tool remains cool, reducing thermal expansion and material deformation.
In our factory, we use a combination of mist cooling and flood coolant systems to ensure that the cutting tool stays lubricated while removing heat from the cutting zone. This helps maintain tight tolerances, as heat buildup can lead to material expansion, causing slight shifts in the part’s dimensions.
Tip: Use a flood or mist coolant system to manage heat and ensure more accurate machining results.
4. Tool Path Optimization for Precision
When working with malleable aluminum, the tool path strategy becomes even more important. CNC machines are programmed to follow specific paths that optimize the interaction between the cutting tool and the workpiece. For malleable materials like aluminum, tool paths should be designed to minimize the amount of material the tool must remove at once. This can help avoid overloading the tool and causing it to wear out prematurely.
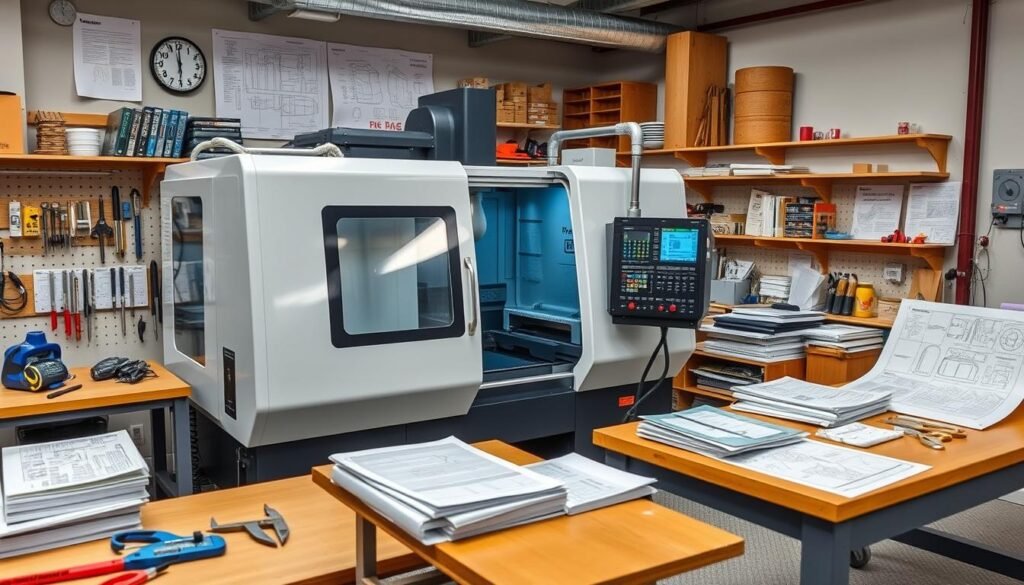
We often use multiple passes when machining aluminum, progressively reducing the material to the desired shape. This technique ensures that the tool doesn’t take too much material in a single pass, which helps in maintaining better control over the precision of the part. Moreover, we rely on advanced CNC software that simulates the machining process, so we can optimize the tool paths before even starting the physical machining process.
Tip: Use multi-pass machining strategies and tool path simulations to reduce tool wear and enhance precision.
5. Clamping and Fixture Design for Stability
One often-overlooked factor when machining malleable aluminum is the clamping and fixture system. Because aluminum can deform under pressure, ensuring that the workpiece is securely held without being over-clamped is essential. If the part is held too tightly, it can shift or distort, especially when subjected to high cutting forces. Conversely, insufficient clamping can cause vibration, which compromises precision.
We use a variety of clamping systems in our shop, including vacuum chucks, precision vises, and custom fixtures designed for specific parts. The goal is to provide enough force to hold the workpiece securely while minimizing the risk of distortion during the machining process.
Tip: Design and use custom fixtures that support the material evenly, avoiding excessive clamping pressure.
Conclusion: Handling Aluminum’s Malleability with CNC Machines
Aluminum’s malleability is both an advantage and a challenge in the world of CNC machining. On the one hand, it allows for intricate designs and the creation of custom parts with high precision. On the other hand, the soft and deformable nature of aluminum requires careful attention to detail during the machining process. From selecting the right tools and adjusting cutting speeds to managing heat buildup and ensuring proper clamping, CNC machinists must take multiple factors into account to ensure that aluminum parts meet the required specifications.
Through years of experience in CNC machining, I’ve found that maintaining the right balance between tool selection, cutting parameters, and material handling is key to producing precision parts from aluminum. Whether you’re working on aerospace components or custom automotive parts, understanding how aluminum’s malleability impacts machining will help you achieve the best results.
If you’re in need of high-precision CNC aluminum parts, we’re here to help. Contact us today to discuss your project and how we can assist with your custom machining needs.
Interested in CNC machining for aluminum or other materials? Subscribe to our newsletter for the latest tips, case studies, and industry insights!